GEM
FASHIONING
Preparing
a gem for use in jewelry, or for display as an ornamental object,
is known as fashioning. In certain cases no fashioning is done
at all; the gem material is used just as it came from Nature.
For example, attractively formed crystal specimens or metal nuggets
are sometimes put on display stands, or mounted in jewelry as
is.
Perhaps
the most common example is pearls. These gems, which are already
in beautiful shapes as found, are occasionally put into their mountings
without even drilling a hole in them.
When
metalsmiths mount an unfashioned gem, strategically placed prongs,
or special adhesives are used to make attractive and secure settings.
The pictures below show some of the ways in which unfashioned
gems are used :
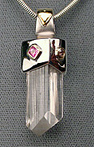
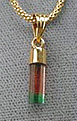
Danburite
and Bicolored tourmaline crystals glued into bezel "cap"settings
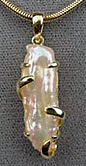
A
baroque freshwater Cultured Pearl set in prongs
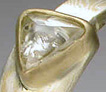
An
uncut/unpolished macle "twin" Diamond crystal bezel
set in a ring
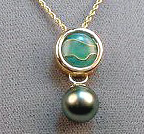
Tahitian
Pearl glued to a dangle setting
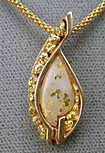
Natural
Gold nuggets soldered into channel setting
Along the same lines as the "Merman"
is the pendant/brooch I recently had made from an unfashioned
baroque freshwater pearl whose shape reminded me of a horse's
head.
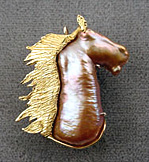
Baroque American freshwater pearl set with prongs and adhesive
in a custom piece by jewelry designer Alex Horst
The
vast majority of gems, however, are fashioned before they are used.
The art and craft of fashioning gemstones is called lapidary (or
diamond cutting), and a practitioner is known as a lapidary, (sometimes
lapidarist), or a diamond cutter.
Here's another instance where we see evidence of the split in the
gem world between diamonds and colored stones; this time it's in
the terminology used to describe the fashioning process, and to
name the craftsperson involved in it.
The
History of Lapidary :
The roots of lapidary go back to the earliest history of human culture.
The first of our ancestors that we can rightly say had "human"
culture, developed crucial skills of knapping (flaking rock edges
to make tools and weapons) and stone masonry. It was not very long
after the fashioning and use of stone and organic materials for
survival needs, that we find evidence of the beginnings of bead
making, carving and engraving using those same materials.
Not only do these artifacts tell archeologists that our remote ancestors
had an aesthetic sense, they also signify how remote are the beginnings
of the social and economic hierarchies so characteristic of humankind.
How long have personal computers been a part our life? Maybe 30
years at most: my own first machine was acquired in 1980. In those
thirty years most of us living in the "modern" world have
learned some rudimentary skills and are using them to accomplish
basic tasks. Some individuals among us, however, have become expert
users of the greatest talent and sophistication. In today's world
it might not be too much of a stretch to say computer savvy is a
survival skill. So....
Imagine a world in which rocks, and certain organic materials like
bone, horn and shell, are not only ubiquitous but also necessary
for survival. That world lasted for many thousands of years and
the consequences of not mastering the technology were far greater
than not getting a high paying job or being unable to download a
tune or write a blog.
During this huge period of time, humans developed highly sophisticated
and successful techniques for working with these minerals and organic
materials. Once the abilities were present, they were passed on,
and improved as part of a people's cultural heritage. But how did
they get started? The most likely answer is that our ancestors put
to use what they saw happening in Nature around them!
Simple observations like the smoothing effect of flowing waters
and their sediments on stones, the sharp edges formed when certain
sorts of rocks broke open, and the realization that some rocks
could make marks or grooves on others could be made every day.
These observations contained the information that led ultimately
to the controlled use of abrasion, cleavage, fracture and hardness
differences to shape, drill and decorate stones.
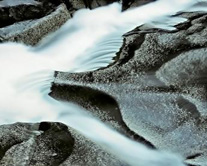
Erosion
at work rounding the edges of rock
It
is not surprising that many of the first tools and ornaments were
of the relatively soft, easy to work organics or minerals, such
as wood, shell, amber, coral, horn, bone, turquoise and soapstone.
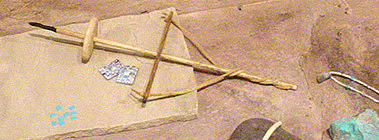
Early
Paiute twist drill for making shell or turquoise beads
One
of the most pervasive themes I've encountered in my own review of
lapidary origins is that the dates for various innovations keep
getting pushed back further into pre-history as new archeological
discoveries are made. Here are some recent examples of that, which,
you might find interesting :
1.
75,000 year old drilled snail shell beads, were recently discovered
in S. Africa, pushed the origin of the first jewelry back 30,000
years earlier than previously documented. (Original article: Henshilwood
et al., Middle Stone Age Shell Beads from South Africa, Science
2004 304: 404 ).
2. Archeologists recently found a polished axe head from China dated
to about 2500 BCE. This tool with a mirror-like shine on its surface
was made largely of corundum. Both logic and laboratory simulations
supported the idea that diamond (the only mineral harder than corundum)
must have been used as the polishing compound prior to this find,
diamond had not previously been documented to be in use until thousands
of years later.
3. Check the web: The first documented use of a "compound
machine" (two or more simple machines used in combination
to do a job), in this case a lathe-like device, comes from the
recent discovery of ancient Chinese jade burial rings, dated to
about 700 BCE, This find, pushes the use of such tools nearly
800 years back from the previously known date of the first century
CE. Original article: Lu, Early Precision Compound Machine from
Ancient China, Science 2004 304: 1638.
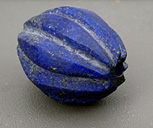
Ancient
Babylonian "melon" bead of lapis lazuli, circa 3000
BCE
Lapidary
Products :
Tumbled
stones :
The simplest of way of fashioning gems, and that which serves as
introduction to a lifelong hobby for many, is tumbling. The tumbler
simulates, but speeds up many-fold, the natural events that make
river stones smooth.
It is accomplished by mixing the rough gems with water and a series
of ever finer abrasives, and either tumbling them in a motorized,
rotating rubber-lined barrel, or subjecting them to prolonged
vibrations.
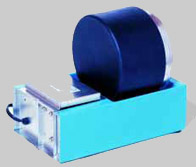
A
Rotary Tumbler
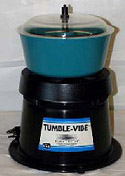
A
Vibratory Tumbler
As the stones hit each other and the abrasive materials, tiny cleavages
and fractures occur slowly rounding sharp edges and corners.
Each
stage (usually 3 or 4) typically takes about two weeks so that
from rough to tumble-polished gems takes considerable time. Tumbling
is not a craft for the impatient. It can also be noisy and messy,
but the product at the end is very pretty.
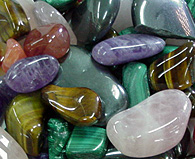
An
assortment of Tumbled stones
The
smooth, shiny tumbled stones can be used as accents in aquaria,
or as decorations in the garden, or in the pots of houseplants.
They can also be glued to "bell cap" findings, and made
into pendants, charms or keychains. They are sometimes drilled to
make baroque beads.
Slabs
and slices :
Sawing, with the exception, perhaps, of tidying up a mineral specimen
or slicing open a geode, is seldom an end in itself, but rather
a preface to polishing or further lapidary work.
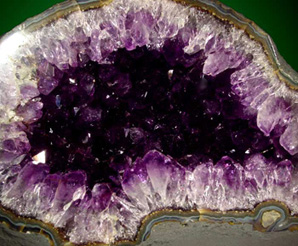
Sawn
Amethyst geode weighing 10.5. lb
Lapidary
saws come in a variety of sizes from tiny facetors' trim saws
with four inch blades, to standard rock slicing saws of 8 - 18
inches, to giant behemoths used to cut boulders.
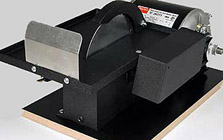
A
small lapidary saw
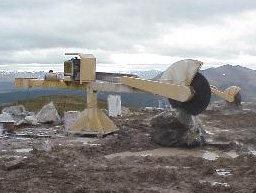
A
giant saw used in preparing jade boulders during the mining process
Unlike
the blades of more familiar wood saws, lapdiary saw blades do
not have teeth per se. In fact, what we call sawing, in lapidary,
is really a grinding process. The blades are generally thin round
disks with an abrasive grit such as silicon carbide, emery, or
diamond embedded into the rim.
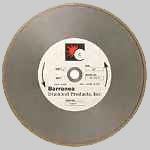
Lapidary
saw blades
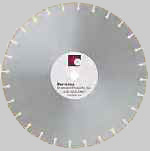
Plain
and Notched
The
rocks may be hand held or, more commonly, secured with a vice.
Such saws must be used with coolant, usually some type of oil,
to dissipate the great heat from the friction generated during
cutting.
Grinding
and Polishing :
Once
a gem has been sawn into slices or trimmed into manageable size,
it is then ground to smoothness and polished to a luster. The
grinding machines employ a metal, or in some cases resin, disk
with its surface or edge covered with abrasives or polishes of
various grit sizes and types. These disks come in two basic styles:
flat "laps" which are used horizontally, and upright
"wheels" which are used vertically.
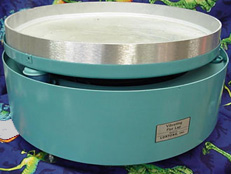
A
horizontal "flat lap" used primarily for slices and
the bases of carvings and cabochons
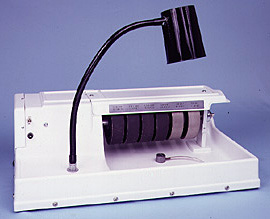
A
combination grinding/polishing unit with vertical "wheels"
used primarily for producing cabochons
The
basic idea here is the same as in tumbling, in that the gem is subjected
to grits of increasing fineness as it is shaped and made smooth,
then finally a polishing compound is applied which produces the
finished shiny surface. The polishes are usually metal oxides or
extremely fine grits of diamond. Various abrasives and polishes
must be used to achieve success with different types of gem materials,
based on their hardness and surface characteristics.
Polished
slices are sometimes used in jewelry, but more often are displayed
as specimens, or ornamental objects such as bookends, wind chimes,
or with translucent material, "sun catchers".
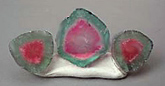
Polished
slices of a bicolored tourmaline crystal will make lovely jewelry
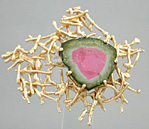
Contemporary
Brooch
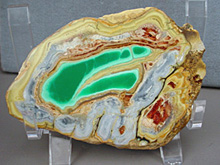
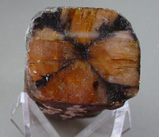
Specimens
of nodular Variscite and Chiastolite with cut and polished front
surfaces used for display
Cabochons
:
Second only to faceted stones in familiarity as lapidary products,
are cabochons (cabs for short). Most commonly cabs have flat bases
and smoothly domed tops, and are fashioned from translucent to opaque
materials. The cabochon form is particularly good at emphasizing
the patterning of a gem, or for displaying most types of optical
phenomena.
They
are usually produced with a slightly beveled bottom edge which
makes for easier and more secure setting in jewelry. Sizes range
from tiny accent gems to large pieces appropriate for use as belt
buckles or in bola ties. Standard shapes such as ovals and rounds
are commonly produced in "calibrated" sizes that fit
exactly into commercial mountings. In other cases, particularly
with rare or valuable material, or those intended for designer
jewelry, the sizes aren't standard, and the shapes may be freeform.
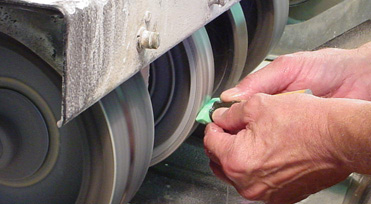
Lapidary
Keith Horst
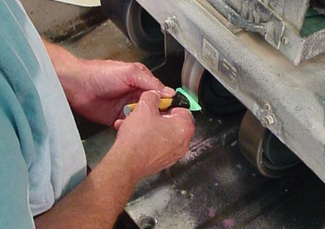
Cutting
a cabochon of Chrysoprase
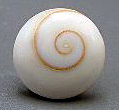
Round
Fossil Ammonite
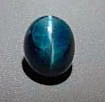
Cat's
Eye Apatite
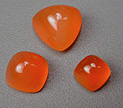
Carnelian
Set
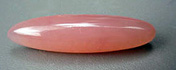
Long
Oval Hydrogrossular Garnet
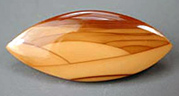
Boat
Shaped Bruneau Jasper
Some
common variants of the cabochon form include gems cut with a series
of curves that meet on top to form an apex rather than a standard
smoothly curved dome, and those whose top is a flat table, a type
usually referred to as a "tablet". Cabs of very dark
translucent material, like deep red almandite garnet, are sometimes
cut with the back hollowed out to lighten their color.
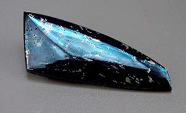
Covellite
cab with an Apex top

Tablets
of Amethyst
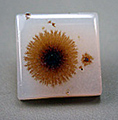
Dendritic
Chalcedony
Beads
:
Beads are one of the most ancient types of fashioned gems, and are
enjoying an enormous resurgence in popularity today. There are beading
magazines and books galore, and most towns of any size have stores
that sell beads along with supplies for stringing them. The Lapidary
Journal, the most widely read, monthly general lapidary magazine,
each year devotes it's October issue to beads.
Beads
are simply gems with holes in them. The fashioning of a round or
other symmetrically shaped bead can be done by hand with cabbing
equipment, but in commercial operations is usually done with a device
called a "bead mill". Sawn slabs are cut into cubes (for
a round bead) and fed into the mill which has grindstones that operate
at angles to the cube removing its edges until it is uniform. Most
mass produced beads then go into a tumbler to be polished and are
drilled with a lapidary drill press, using diamond tipped drill
bits.
The
hole can be completely through the gem, or only part way through,
in which case it is said to be "half drilled". Most commonly
half drilled beads are used for stud earrings, rings or dangles.
Depending on which direction they are drilled (side to side or top
to bottom), and whether the drilling is centered or not, full drilled
beads find various uses such as in bead strands and as dangles.
Beads
can be virtually any shape : round, oblong, tubular, flattened
circles (rondells), briolettes, fancy or baroque.
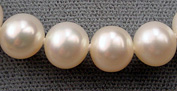
Side
to side drilled Pearls
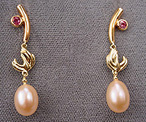
Half
drilled Pearls
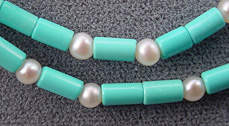
Tubular
Turquoise beads with Pearls
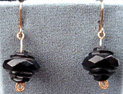
Top
to bottom drilled Jet beads for dangles
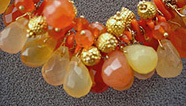
Non-centered
side to side drilled Carnelian briolettes for dangles
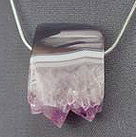
Fancy
Cabochon bead

Rondell
strand of Mexican Opal
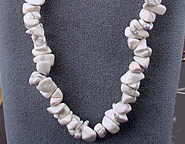
Baroque
(tumbled) bead strand of Howlite
Engraved
and Carved Gems :
Gems fashioned by engraving are incised, so that a design is cut
(shallow or deep) into their surface, whereas carved gems are fully
three-dimensional.
Engraving
and carving should be considered lapidary arts rather than crafts,
as the vast majority of styles and pieces can only be done well
if the maker has some degree of artistic talent, an ability not
required of those doing tumbling, cabbing, or bead making. Although
the majority of such pieces are orginal works of art, more and more
use is being made, especially in commercial production of gem carvings,
of ultrasonics and lasers which are sometimes computer-assisted,
and may be used to produce many exact replicas of a single original
carving.
Engraving
and carving gems is, like bead making, a very early form of lapidary.
Historically, such pieces were done by hand with bone, stone, or
metal tools and suitable abrasives. The choice of tools was dependent
on what was locally available, and on the hardness of the material
being worked. There are still a few hand carvers who carry on this
tradition. For the most part, though, today's gem carvers and engravers
use electrically powered tools with silicon carbide or diamond tipped
implements.
One
of the most commonly used tools for carving and engraving is the
"flex shaft" which consists of a motor which drives
a pen-like device with a rotary head that can be fitted with dozens
of different cutting, drilling, carving, sanding and polishing
tools.

A
flex shaft tool with an assortment of "bits"
When
using a flex shaft, which is usually hung on a stand and operated
by a foot switch, the item being worked is mounted in a vice or
held stationary in some way while the rotary tool, held like a pen
in the hand, is used to grind or polish it.
Alternatively,
many artists favor a reversal of this system whereby a "fixed
arbor" which contains the rotating tools sits on their bench,
while they hold the item to be carved in their fingers, and apply
it to the tool.
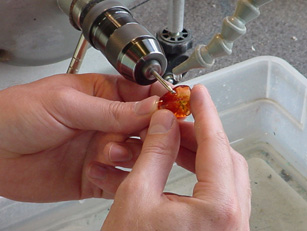
A fixed arbor for carving a Citrine note water drip
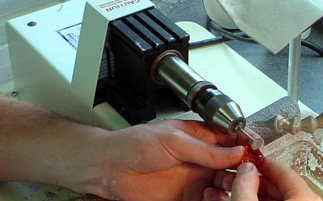
Differently
shaped diamond tools
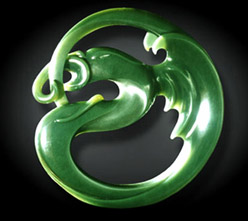
With
such a long history, it is not surprising that a large number of
different carving styles, as described below, have been developed
and made popular.
1. Intaglio :
In these gems, a design is cut into the gem, so that it lies below
the rest of the gem's surface. Historically they were worn in
a ring which was also used to form a signature seal. Intaglios
have always been most popular in men's jewelry.
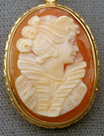
Contemporary
shell Cameo
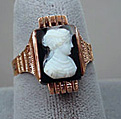
Antique
"hardstone" Agate Cameo ring
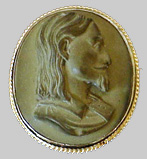
Victorian
Lava
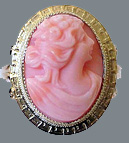
Coral
Cameos
3.
Scrimshaw :
In this technique a design is shallowly engraved into the surface
of horn, bone or ivory then inked, or painted to provide contrast
or color. Scrimshanders have a long history, particularly among
those peoples who traditionally hunt either marine mammals, elephants,
or other herbivores with antlers, horns or sizeable teeth or tusks.
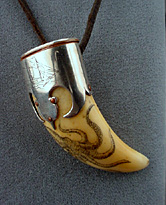
A
19th century American sperm whale tooth scrimshaw pendant
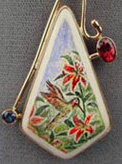
Contemporary
painted scrimshaw (on legally collected elephant ivory)
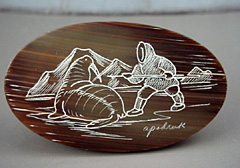
Contemporary
Native American scrimshaw (on legally collected whale baleen)
4.
Surface engraving/carving :
In this technique a cabochon is decorated with designs carved into
it (front, back or all round). Highly transparent material is sometimes
"reverse" carved where the design, usually left unpolished,
is cut into the back to create a picture visible from the front.
The three dimensional scenes which result require great skill to
accomplish, and can be stunningly beautiful.
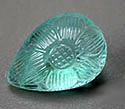
Surface
carved Aquamarine
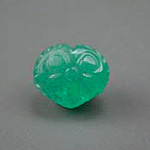
Emerald
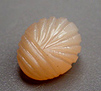
Moonstone
Cabochons
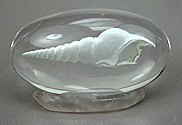
Carved
rock Crystal Quartz
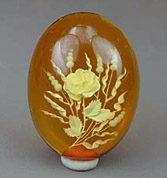
Amber
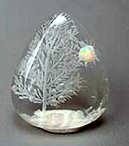
Rock
Crystal Quartz
5.
True Carving :
When the cutting or engraving work encompasses all sides of the
piece so that it's truly three dimensional, it is said to be a carving.
The four most common styles for carvings are hololith, representational,
stylized, and abstract.
Hololiths
are hollow, three dimensional jewelry pieces, usually rings or bangle
bracelets that have been carved from a single piece of stone. Some
of the most charming of these consist of two or more interlocked
pieces.
Representational
carvings are meant to resemble the subject as closely as possible.
In stylized carvings, we recognize the subject matter, but the artist
has put their own interpretation on it. Abstract carvings are made
as pure expressions of form with no overt reference to real objects.
HOLOLITHS
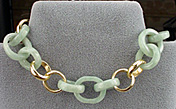
Jadeite
interlock bracelet
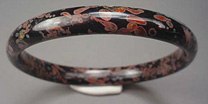
A
Poppy Jasper bangle bracelet
REPRESENTATIONAL
CARVINGS
Chalcedony
Octopus
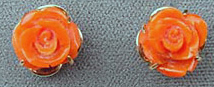
Coral
Roses
STYLIZED
CARVINGS
Lapis Lazuli rattlesnake tail
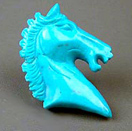
Turquoise
Horse
ABSTRACT
CARVINGS
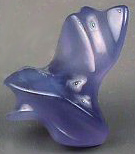
Blue Chalcedony
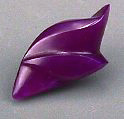
Sugilite
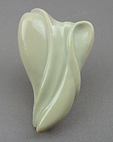
Jasper
Faceted
Gems :
The most popular fashioning style for transparent gem material is
the faceted gem. Because colored stones and diamonds are cut by
different methods, and graded and marketed separately, we'll look
at each in turn, although some of what is covered below applies
to both.
Colored
stones :
When discussing a faceted stone, the first distinction that is often
made is shape (face up outline). As is also true of diamonds, colored
stones are either rounds or fancy cuts. So ovals, pears, freeforms,
etc. are all "fancy". Going beyond the outline shape,
one might next look at the cutting style. There are three traditional
basic styles (brilliant cut, step cut and mixed cut), with many
old and new variations upon them.
The brilliant cut which is especially suited for producing light
return to the eye (brilliance), has triangular and kite shaped
facets. The step cut, which is more suited for emphasizing color
in a gem, has tiers of rectangular to square facets. Mixed cuts
usually have a brilliant style crown with a step cut pavilion,
but the opposite arrangement can be seen as well. Occasional variants
include faceted gems with an apex rather than a flat table, and
those whose crown is formed of rows of parallel facets (opposed
bar cut) or a field of intersecting squares or diamonds (checkerboard
cut).
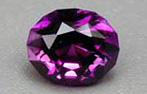
Oval
brilliant cut Amethyst
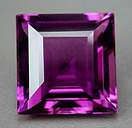
Square
step cut Amethyst
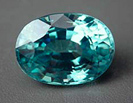
Oval
mixed cut Blue Zircon
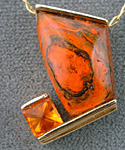
Apex
cut square Mexican opal
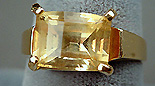
Rectangular
opposed bar cut Citrine
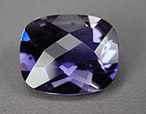
Rectangular
cushion checkerboard cut Iolite
Less
frequently seen variations of the faceted gem are buff tops, briolettes,
concaved cuts and fantasy cuts. A buff top gem has a faceted pavilion
with a smoothly domed (cabbed) crown. An interesting magnifying
effect of the pavilion facets is achieved by doing this. The briolette
(mentioned earlier as a popular bead style) is a three dimensionally
faceted gem, usually in a pear or tear drop shape. Concave cuts
have, logically, concaved or sunken in facets on either the crown
or pavilion or both. This technique increases overall light return
and creates unusual reflective patterns and/or face-up outlines.
The "laps" which are used for concave cutting are cylindrical.
Relatively few facetors have the equipment and expertise necessary
to produce stones of this sort. Extra time to attain a good polish,
and more expensive equipment are two factors which tend to set
a premium price for such gems. Fantasy cuts have carved areas
on the crown or pavillion, which may be polished, or left unpolished
to create special effects.
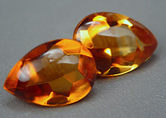
Buff
top pear shaped Citrines
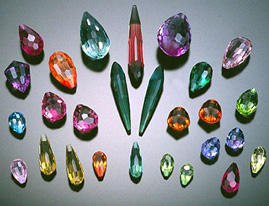
A
selection of Briolettes
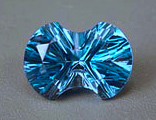
Concave cut Swiss Blue Topaz, showing both the dramatic
reflective pattern and the"scalloped" outline which
can be seen in concaved gems
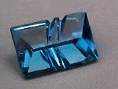
Fantasy
cut London Blue Topaz
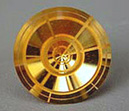
Fantasy
cut Citrine with unpolished carved channels on the pavilion to
create a "bullseye" effect
The
Faceting Process :
Faceting
is the newest of the major lapidary crafts. Historically, we don't
find the first faceted gems until the 14th century and faceted diamonds
don't make an appearance until the 16th century. The earliest cuts
were done by hand, and had just a few facets. An example of an early,
but still occasionally used cut, is the rose cut which was often
chosen for early diamond jewelry. The rose cut has a flat bottom
like a cabochon, with a series of facets rising to form a dome or
apex.
Several
hundred years ago the jamb peg faceting machine came into use,
and faceting, as we recognize it today, began. In order to cut
facets on a gem in an organized manner that results in a precise
arrangement, three factors must be controlled: 1) the angle of
the cut 2) the depth of the cut and 3) the radial placement of
the cut. Although modern highly engineered faceting machines have
replaced jamb pegs in much of the world, these older systems are
still widely used, and a substantial proportion of the gems in
commerce today have been cut by them.
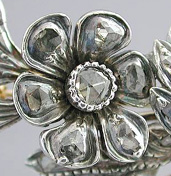
Typical
antique rose cut Diamonds in a circa 1840 brooch (the diamonds
in this piece were probably already antique when it was made)
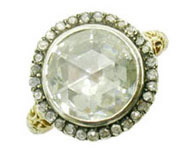
A
modern-day rose cut Diamond in a contemporary "antique style"
ring
Background
Information on Faceting :
Pavilion
and Crown: In the faceted gem, the pavilion and crown have different
functions. The crown acts as a window or lens to collect the light
which strikes it, and direct or focus it into the pavilion of the
gem, whereas the pavilion must act as a mirror to reflect that light
around the pavilion, and then back to our eyes through the crown.
If the pavilion fails to do so, the gem lacks brilliance and is
lifeless. Crown angles are much less crucial to the optical performance
of a gem than are those of the pavilion, and can vary substantially
from stone to stone without severely affecting a gem's brilliance.
The crown and pavilion are cut in two separate sequences of operations.
The gem is initially adhered to the "dop stick" until
one side is finished, then removed, turned exactly 180 degrees,
and attached to a new dop, to go through corresponding operations
for the other side.
The
Critical Angle :
Each gem species, depending (with an inverse relationship) on its
refractive index, has a pavilion faceting angle below which it loses
brilliance.
Think for a moment of skipping flat stones on water. What controls
whether the stone will skim and bounce along the surface, or go
kerplunk into the depths?.......The angle at which it hits the water!
So it is with light that enters a gem and strikes the pavilion facets.
When that beam hits outside the crtical angle it will be reflected
to another facet and/or to the crown, but if it hits inside the
critical angle it will not reflect, but pass right out through the
side or bottom of the gem, not to return to our eye the gem loses
brilliance.
In
the graphics below we see two gems cut to the same proportions
(pavilion main angles at 38 degrees) one is a diamond (RI = 2.42),
the other is a fluorite (RI = 1.43). The critical angle for diamond
is about 24 degrees, that of fluorite is 44 degrees. At 38 degrees
on the pavilion facets much of the light hitting the fluorite
is lost, whereas almost all that which hits the diamond is reflected.
The diamond would appear bright and the fluorite lifeless, especially
in the center: we would say it has a "window". If, instead,
we were to cut the fluorite to a pavilion angle of 45 degrees
or above, we would then eliminate the window and it would be brilliant,
and conversely we would get a lifeless diamond if we were to cut
its pavilion at 20 degrees or below.
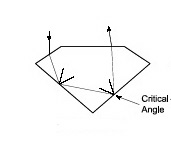
Reflection
when the pavilion angle is above the critical angle
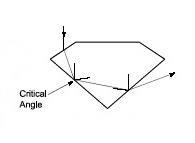
Lack
of reflection "windowing" when it is not
In
the first picture below you can see two similar looking gems (each
is light yellow and rectangular). The golden beryl gem on the
left was cut with its pavilion facets above its critical angle,
and it appears brilliant, the yellow spodumene on the right was
cut with the pavilion facets below its critical angle and has
a "window". We call it a window because the light passes
right through it, like window glass, so that you can easily read
the printing underneath. The second set of pictures shows a top
and bottom view of a badly windowed topaz. You can see how shallow
(low angle) the pavilion is. In order for this gem to be fully
brilliant, the necessary recutting would reduce it's face up diameter
and carat weight substantially.
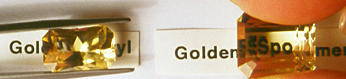
Non-windowed
and windowed gems
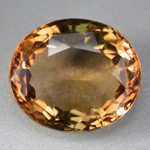
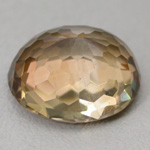
A windowed topaz gem with a very shallow paviliont
Yield
vs Brilliance, Clarity and Color :
Faceting is a series of compromises. The yield, that is the carat
weight, of the finished stone versus he carat weight of the rough,
can be as high as 40 - 50% or as low as 1-2% depending on a mix
of the attributes of the rough, and of decisions that are deliberately
made by the facetor.
For
example :
1. The shallower the pavilion angles, the greater the yield
(but the less the brilliance).
2. Included rough can be oriented (with loss of yield) to eliminate
or minimize the appearance of inclusions.3. Pleochroic stones will
give different colors and different yields depending on how the
stone isoriented for cutting.
4. Rough that happens to be somewhat "gem shaped" yields
more than thin and flat, or highly asymmetrical rough. Given a
moderately well shaped, clean piece of rough, which is cut to
correct pavilion angles, the average yield is about 20%. To put
it another way: start with gem rough = 5 ct, end up with finishedgem
= 1 ct.
Faceting Tools :
In the figure below you can see the basic set up of a
traditional jamb peg faceter. The spinning lap provides the grinding
and polishing surface, the wooden "dop" sticks to which
the rough is adhered, serve to hold the stone in position as various
cuts are made. The angle of the cut is controlled byplacing the
dop stick in a particular hole, the depth of cut is controlled
by the amount of time the piece spends in contact with the lap
and how hard the facetor presses down on it, and the radial position
is controlled by removing, slightly rotating, and reinserting
the dopstick in its hole as each different cut is made. Most stones
that are cut on such equipment are referred to as "native
cut".
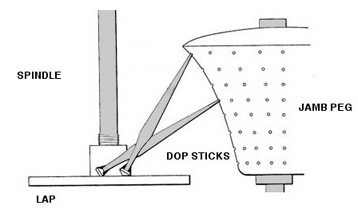
A
jamb peg faceting machine
A
modern, highly engineered faceting machine is seen below: such machines
accomplish the same three goals (angle, depth, and radial position
of facets), but do so with great accuracy. In machines of this type
the dop stick with the gem attached to it, is fitted into a "quill"
which can be postioned at various precise angles via the "protractor".
The quill moves up and down on the mast, which gives great control
over the depth of cut, and a slotted index gear gives accurate control
over the radial placement of facets. Stones cut on such equipment
are usually described as "custom cut".
Before summarizing the differences between the products of the
two types of machines (which is going to make the native cut gems
sound pretty lame), let me say that it takes long training, and
tremendous skill to be able to produce a nice looking gem with
a jamb peg, whereas virtually anyone who can read the lapidary
equivalent of a cookbook can produce an acceptable stone with
modern machinery!
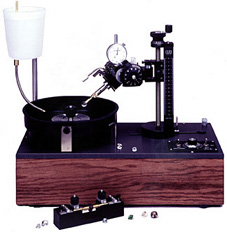
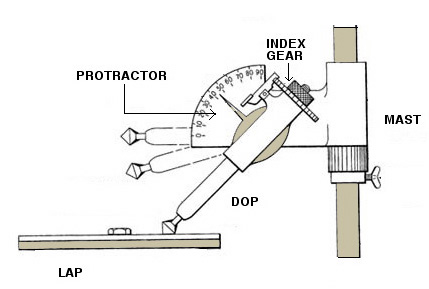
A
typical modern faceting machine
Native
cut gems :
These are generally cut by eye, usually in Asia, Africa or S. America,
on a lap, or more often a jamb peg or similar machine. The cuts
are typically oval to cushion shaped with windows, low crowns and
bellied pavilions. The "make" (proportions and finish)
is "inferior" in that the table sizes, crown heights,
pavilion depths, facet meets and degree of polish are not to custom
standards.
Such
cuts give high yield from gem rough, and due to the increased volume/mass
of the pavilion tend to deepen and emphasize color. For these reasons
the majority of the high value colored gem rough (ruby, sapphire,
emerald, Imperial topaz, etc) is still cut this way even though
the cutters could make smaller, brighter stones with the equipment
they have. Frequently native cutters are paid by yield, another
factor which perpetuates the native style of cutting.
A
few native cutters working in certain gem factories (such as the
one pictured below) pride themselves on producing custom-style
gems, a feat all the more impressive given the equipment available
to them. Every angle and facet placement is determined by eye
alone.
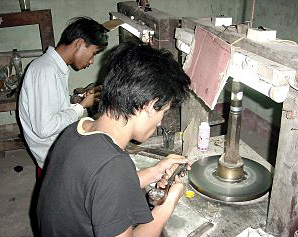
Native
cutters in Vietnam, working on spinel and ruby, one of their custom-style
gems
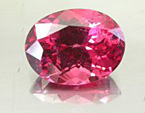
A
pink spinel
Custom
cut gems :
These are usually produced on some type of precision engineered
faceting machine (there are many brands), usually in N. America
or Europe, using magnification. Cuts can be any shape, but are characterized
by "superior make". The gems are usually fully brilliant
with no windows and pleasing crown to pavilion proportions. The
level of polish, and the precision of facet meets is very fine.
Such cutting sacrifices yield, and may lighten the color tone of
gem material. On the other hand custom cut stones are generally
easier to set in commercial mountings, and extremely beautiful due
to their brilliance and symmetry.
Faceting
Paraphernalia :
Various
adhesives are used in faceting, such as epoxy resin, cyanoacrilate
"Super Glue", and faceting wax. Different gem cuts require
different index gears, the one below has 96 slots and can cut
gems with 3, 4, 6, 8, 12 and 16-fold symmetries (other indices
would be used for gems with 5 or 7-fold symmetries). The dops
are commonly made of brass and come in a large variety of sizes.
Seen below are three: a flat, a cone, and a "vee". Each
is used for rough of certain shapes, or during different points
in the faceting process.
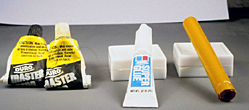
Lapidary
adhesives (epoxy, "super glue" and facetors' wax)
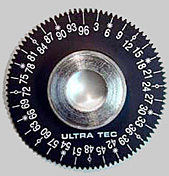
Afaceting
index gear
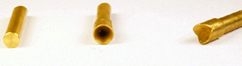
Brass
Dops
The
laps used for cutting and polishing come in a variety of materials
and sizes. The first picture below shows two diamond-surfaced
cutting laps: the one on the left has a coarse diamond grit embedded
into its metal surface, it would be used to lay in the basic shapes
of the facets, the other one has finer grit and would be used
to smooth the facets and prepare them for polishing. The second
picture shows a polishing lap which is made of a plastic resin
with fine metal particles embedded in it, very fine grit diamonds
(in solution) are sprayed onto the lap surface for polishing the
gem. Metal oxide slurries or sprays (such as cerium or aluminum
oxides) can also be used for some gem materials.
DIAMIND
CUTTING LAPS
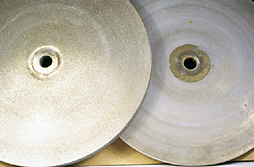
Coarse
and Fine
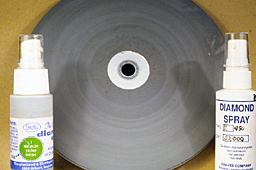
Resin-metal
gem polishing lap with diamond sprays
The
"faceting cookbook" :
Although some facetors do freehand cutting or design and execute
their own special cuts, most follow diagrams that indicate the angles,
number and cutting sequences for the facets. (Due to critical angle
differences, the directions for a round brilliant topaz would have
slightly different angles than those for a round brilliant quartz).
In the graphic below "B" = bezel facets, "M"
= main facets, "S" = star facets, and "T"
= table. ID indicates the "12 o'clock position" for
the index gear. (On the left is the pavilion cutting diagram,
and on the right the crown cutting diagram).
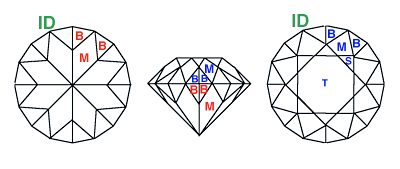
Round
brilliant faceting diagram
For
example, the first instruction in such a facetor's "cookbook"
might say (for quartz) "Cut 8 equidistant 42 degree facets
as the pavilion mains, so that they meet to form a culet".
This would be followed by something like: "At index settings
on either side of the main facets, cut 16 bezel facets at 44 degrees".
The directions would continue through the entire cutting process
like following a recipe in a cookbook.
Actually, there is a bit of finesse to it, and quite a lot to
learn, but faceting is nothing which requires high level mechanical,
manual dexerity, or mathematical skills, and is enjoyed by many
as an interesting hobby.
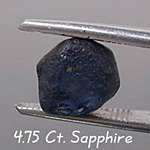
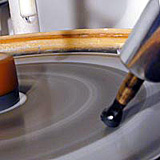
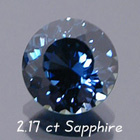
From
rough Sapphire to custom faceted gem
To
emphasize my point that faceting should not be viewed as an especially
intimidating craft, here's a picture of a successful new facetor:
the 10 year old grandson of well respected cutter, Barry Bridgestock.
The stone shown is his second production, and he did have guidance
from Grandpa but not bad.
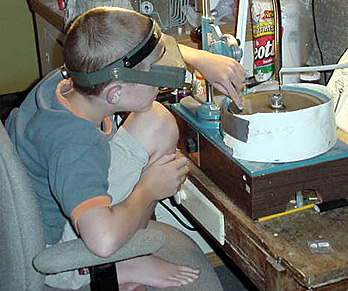
Jake Bridgestock, Age 10, Facetor
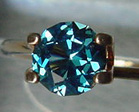
A
Blue Topaz cut by Jake
Diamond
cutting :
Considerably more talent and expertise is necessary for diamond
cutting than that required of the colored stone facetor. In order
to successfully cut diamonds one must be able to look at a piece
of rough and determine its crystallographic axes. This knowledge
is then used in choosing the best cut to use, as well as in orienting
and cutting the various facets, which must be ground in different
directions on the lap, depending on their variable hardness.
The
cutters must be adept at getting maximum yield while still retaining
good brilliance. A 1-2% difference in yield would be small potatoes
for most colored gem cutters, but in the case of a diamond, many
dollars could hinge on it.
A
"natural", a small unpolished area left on the girdle
of a diamond, far from being a blemish, is a considered a sign of
superior cutting meaning that the cutter has gotten the biggest
stone possible from a particular piece of rough. In today's diamond
cutting industry computerized angle analysis, and computer assisted
design (CAD), is often used to help cutters maximize yields.
In
order to get the highest yields, most diamonds are cut with slight
to moderate deviations from the "ideal" proportions, resulting
in some loss of brilliance and/or dispersion. There are diamond
cutting firms, though, which specialize in "ideal cut"
diamonds. These stones are, on average, at least 10% more expensive
per carat than "run of the mill" diamonds. In truth, only
a well trained eye can detect these subtle differences in proportions,
dispersion and brilliance, but as with any product, there are those
who are eager to have the "very best", and quite are willing
to pay extra for it.
The
equipment used in diamond cutting is heavy duty, reflecting the
tremendous forces and long periods of time necessary to cut and
polish this hardest of all materials. The lap, called a "scaife",
is made of cast iron, and revolves at about 3000 rpm. Diamond "bort",
in oil, is used for cutting and polishing. The stone is held by
a "tang" which is a claw-like mechanism (no adhesive could
withstand the intense heat generated by cutting).
The
cutting and polishing process is really one of simple (but painstaking)
abrasion as the tiny diamond crystals in the oil, being forced against
the rough with great speed and pressure, successively wear away
minute bits of diamond from the surface, gradually making it more
smooth and uniform. Because the bort particles are randomly oriented,
there are always at least some whose exposed crytal faces are harder
than the surface to be polished (this is true as long as the diamond
has been properly oriented for cutting to begin with its own hardest
crystallographic axis cannot be directly parallel to any facet.)
The
directions in which a diamond can be polished are called its "grain"
and there are three basic types of rough (and many variations on
those) each with a different pattern of grain directions. During
the cutting process, as the different grain areas are brought to
the scaife, the direction of the polishing must be altered. Twinning
in diamonds can greatly complicate the cutting process as there
will be an overlapping of harder and softer axes. Only a few firms
specialize in cutting twinned crystals.
Diamond
cutting centers in New York, Mumbai, Antwerp, and Tel Aviv produce
the large majority of the world's diamond gems.
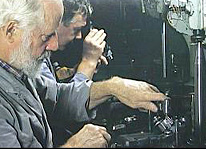
Cutters in a Diamond factory in Antwerp
Although
there certainly are "master" cutters who can start with
a piece of diamond rough, and go through all the steps to produce
a finished gem; in the commerical world of diamond production, the
process is usually divided into stages, each of which is accomplished
by a specialist in that part of cutting.
1. Marking :
The "marker" studies and then marks the rough to direct
the removal of inclusions, and indicate how the piece should be
cleaved or sawn. For large, extremely valuable pieces, this stage
may take weeks or months.
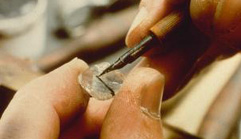
A
Diamond being prepared for cleaving or sawing by the "marker"
2.
Cleaving and/or sawing :
Although most of us can picture that tense moment when the "cleaver"
swings his mallet and strikes the wedge that will separate a diamond
along its cleavage plane, in reality, few diamonds are cleaved
today. The average piece of rough is sawn (by diamond blade or
laser) into suitably sized and shaped pieces by the "sawyer".
Cleaving is still important with large rough however.
A
Diamond being cleaved
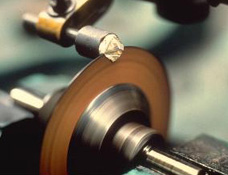
A
Diamond being sawn
3.
Bruting :
The job of the "bruter" is to create the face up outline
of the gem: round, oval, marquis, etc. The time honored technique
for doing this involves using one diamond to grind another and
is done mostly by eye using a lathe-like apparatus. When bruting
is done with too much force, or too much heat is allowed to build
up, tiny whisker-like feathers can be seen around the girdle of
the stone. This is a blemish called a "bearded girdle".
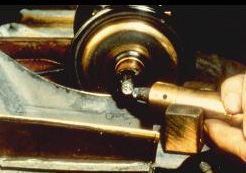
The
bruting process
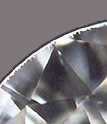
A
Diamond with a "bearded" girdle
4
& 5 Blocking & Brillianteering :
The "blocker's" job is to create the basic shape and
proportions of the gem by cutting the table and culet as well
as the crown and pavilion main facets. The "brillianteer"
(the cutting superstar), traditionally puts in the stars, and
the crown and pavilion bezel facets, each one of which may require
subtle adjustments of angle, direction and size, depending on
the grain pattern of the individual stone, its inclusions, and
the desired cut.
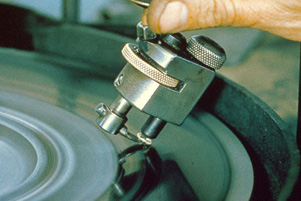
A
diamond in the cutting process, note the tang holder and the spinning
scaife
BEFORE AND AFTER
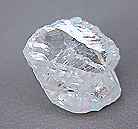
A
rough Diamond
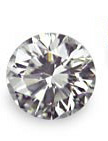
A
brilliant cut Diamond